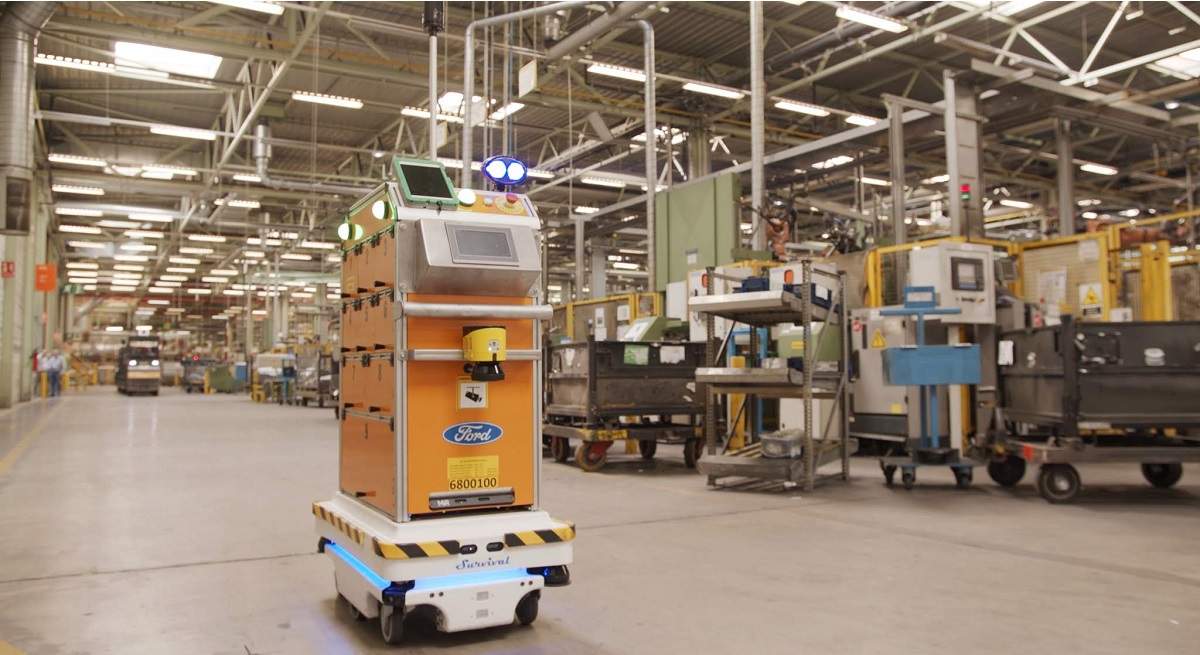
Ford ha vuelto a poner a prueba a sus factorías en Europa para decidir cuales son las que pasarán la criba que supone la introducción del coche eléctrico. Un examen crucial que la planta valenciana de Almussafes ha logrado aprobar al ser capaz de superar a la fábrica alemana de Saarlouis en la guerra por reducir los costes céntimo a céntimo.
Una obsesión que la filial valenciana lleva a su máxima expresión también en la innovación, donde concentra sus esfuerzos en lograr ahorros superiores al 30% en su impacto económico y en el 50% en lo que se refiere a tiempos.
La factoría de Almussafes aposto por unirse a sus proveedores directamente con un tren elevado o conveyor y fue la primera del grupo que incluyó además de la fabricación el mantenimiento integrado. Durante el año 2022 la planta ha puesto en marcha 169 proyectos de investigación y desarrollo propios para ganar eficiencia en su producción industrial y logística.
Entre las iniciativas que mayores réditos le han dado se encuentran las de impresión 3D y fabricación aditiva, en que la filial valenciana ha conseguido ahorros de entre el 80% y el 90% en los costes algunas piezas y recambios de los equipos que utiliza diariamente en sus líneas, según desvelaron los técnicos de la propia compañía durante el Ford I+Day, en que se pusieron de largo varias de esas iniciativas.
Uno de los casos concretos ha sido su aplicación a lo que en la jerga de la planta de automóviles se denominan las cunas de los motores: los recipientes que se utilizan durante el proceso de montaje y el transporte de los equipos que son el corazón de cada coche. Cada cuna fabricada en metal pesa 60 kilos para poder poder aguantar los motores. Sin embargo, ante la necesidad de producir recambios con el uso de las impresoras 3D ahora se han diseñado y fabricado cunas de plástico de apenas dos kilos con una reducción de costes del 85%.
La factoría valenciana cuenta con su propia unidad de impresión digital, con 15 máquinas capaces de utilizar todo tipo de materiales, y este área de innovacion se ha convertido en una de sus grandes estrellas, con un proyecto que busca convertir a la factoría en autosuficiente en lo que se refiere a poder fabricarse por sí misma todos los recambios de sus equipos y maquinaria de producción, como sus propios robots. De hecho, otro de sus proyectos se ha centrado en utilizar esta tecnología para producir y mejorar los grippers o garras de los robots de sus líneas automáticas.
Según Javier Igual, ingeniero de Aplicaciones y Gestión de Fabricación Aditiva, esta tecnología ofrece ventajas más allá de la reducción de costes, como la posibilidad de alargar la vida de maquinaria obsoleta porque sus repuestos están descatalogados o reducir notablemente los tiempos de espera, esenciales en las líneas de montaje del automóvil como se ha demostrado con la crisis de la cadena de suministro.
Otro de los campos en los que Ford Almussafes ha experimentado es en la impresión de referencias de metal y en la producción de componentes con distintos materiales simultáneamente. Unos desarrollos que ya le han permitido conseguir ahorros en determinadas piezas de entre el 80% y el 90% con materiales como el titanio.
Planta sin conductores
Entre los siete pilares o grandes áreas de innovación en que la filial española marca el paso en Ford se encuentra el uso de los vehículos autónomos para logística interna. La planta de motores de Valencia se ha convertido en la primera del grupo en la que no circulan carretillas o convoyes con un conductor al volante, ya que este año se han reemplazado en su totalidad por vehículos automáticos de guiado (AVG por sus siglas en inglés).
En el complejo de Almussafes ya circulan 142 vehículos de este tipo, fabricados por 8 proveedores distintos y que transportan todo tipo de piezas a sus líneas de ensamblaje. "Tenemos implantadas más de 45 rutas automatizadas y los AVG realizan 160.000 kilómetros al año, el equivalente a cuatro vueltas al mundo", según Eugenia Vallet, ingeniera y responsable de este área de innovación. Un éxito que también ha hecho que el equipo valenciano haya sido encargado de diseñar los estándares que utilizará Ford Europa en esta tecnología.
El siguiente paso en el que trabaja es en conectar sus distintas instalaciones dentro del complejo valenciano. En concreto, unir la planta de motores y la de baterías híbridas con las líneas de montaje de los coches, de forma que puedan circular por viales que también utilizan camiones y vehículos tradicionales. Además de reducir tiempos y costes, la planta utiliza la tecnología para mejorar su seguridad, como el proyecto Moisés. Un sistema por el que los vehículos autónomos se apartan ante una ambulancia o camión de bomberos.
Un arsenal con el que Almussafes afronta el salto al coche eléctrico, otra "reconversión", en la que "el mercado no te va a perdonar no ir", según el director de Fabricación de Ford España, Dionisio Campos.