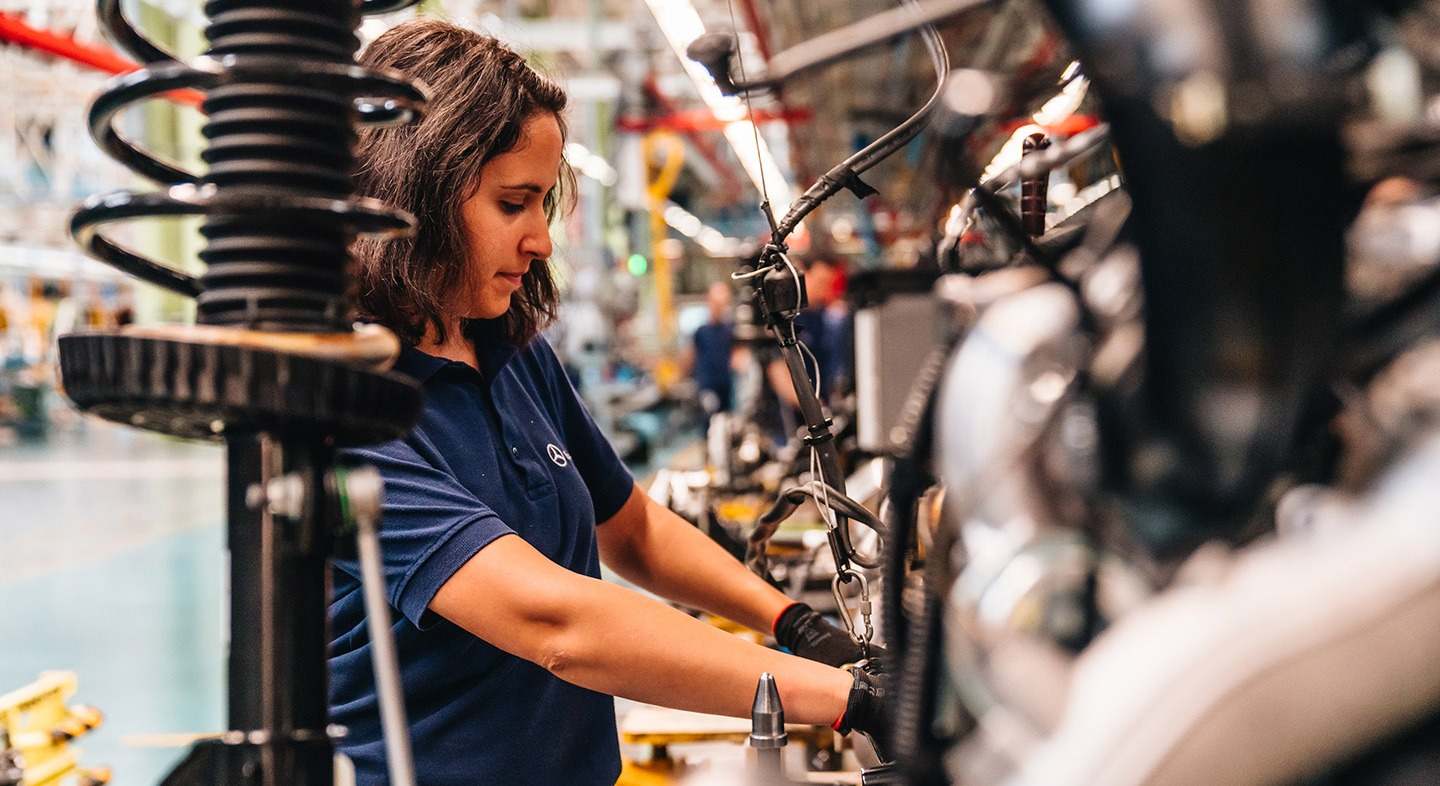
Mercedes-Benz España y Ayesa están trabajando en un proyecto que busca lograr cero errores en el proceso de ensamblaje de automóviles y alcanzar la excelencia en su sistema de producción. Para ello, el proveedor de soluciones tecnológicas, ha desarrollado una plataforma cuántica capaz de detectar automáticamente cualquier anomalía de configuración, con varios días de antelación a que los coches entre en las líneas de fabricación.
El entorno de producción de vehículos industriales de Mercedes-Benz es muy característico, ya que cada coche cuenta con una configuración individualizada no seriada, en función de las preferencias de cada cliente. Estas individualizaciones entran en el sistema en forma de una lista de códigos que representan las solicitudes realizadas por el cliente, por lo que cada lista define completamente un automóvil a producir.
Hasta ahora el sistema de pedidos trataba de prohibir las combinaciones de códigos que pudieran causar problemas durante la producción, pero debido al alto grado de complejidad por la cantidad de variables existentes, puede haber códigos que definan un automóvil que no se pueda producir. El sistema de Ayesa identifica los coches que no se pueden fabricar, basándose en estos códigos, antes de entrar en la cadena de producción.
El modelo cuántico desarrollado genera un sistema automático para la detección de configuraciones "anómalas" en diferentes niveles jerárquicos, como el nivel de pedido, el de producción, el de modificaciones, el de proceso, y la comparación de diferencias entre "estados anómalos" y "estados similares" en la misma fecha.
El sistema verifica si la diferencia detectada es correcta, y en caso contrario se emite una notificación de posible error, antes de que dicha incidencia colapse las líneas de producción en una planta real. De esta manera, Mercedes-Benz se aproxima a los cero errores en el proceso de ensamblaje de automóviles, lo que significa mejorar al máximo la excelencia de los sistemas de producción actuales.
La prueba de concepto se ha llevado a cabo en la planta de fabricación de Mercedes-Benz en Vitoria. El sistema está utilizando una base de datos de entrenamiento, con 50.000 pedidos (50.000 filas) y cada pedido con 706 características diferentes, es decir, componentes de automóviles, y cada día se comparan 14.000 pedidos (conjunto de prueba) con el conjunto de entrenamiento detectando pedidos anómalos.
Motor económico para Euskadi
A lo largo de sus 70 años de historia, Mercedes-Benz Vitoria se ha consolidado como un motor económico para Euskadi y España, ya que genera empleo directo para 5.000 personas en la planta de Vitoria y alrededor 30.000 empleos indirectos, e implica a 800 proveedores de componentes de automoción en todo el país.
La fábrica de Vitoria se encuentra inmersa en un proceso de adecuación y transformación de sus instalaciones para producir las nuevas furgonetas medianas basadas en la nueva arquitectura eléctrica, modular y escalable -VAN.EA-, cuya implantación marca el rumbo hacia un futuro eléctrico.
No obstante, la planta de Mercedes Benz en Vitoria está adaptando su producción a la demanda actual y reducirá media hora el turno de noche en los sectores de montaje bruto y montaje final a partir de hoy lunes. Esta medida se adopta con el objeto de optimizar la capacidad productiva actual de la fábrica y el flujo de suministro interno de vehículos.
Relacionados
- Mercedes-Benz España incrementa su beneficio un 8,9% en 2023 hasta los 105,2 millones
- Seat, Envision y Mercedes-Benz copan la mitad de las ayudas de los Perte VEC
- Mercedes ratifica su apuesta por la planta de Vitoria con 1.000 millones para producir eléctricos
- Mercedes Vitoria comenzará en marzo la producción de las nuevas furgonetas Vito y eVito