Renault ha escalado su plan estratégico industrial para competir con los fabricantes asiáticos en reducción de costes de producción y digitalización de sus plantas. En dos años, el grupo ha implantado en su planta española en Palencia tecnologías como inteligencia artificial, la automatización, el uso de robots y un metaverso que le permite monitorear en tiempo real producción de cada planta, vehículo y herramienta que tiene el mundo.
El grupo francés ha desarrollado en los últimos dos años un sistema con inteligencia artificial en sus plantas que, a través del análisis de datos en tiempo real, permite una gestión automatizada de los procesos de producción y control de calidad, desde el momento en que se encarga un vehículo en un concesionario hasta la entrega. El hub instalado tanto en su planta de Valladolid, como en la de Palencia, procesa hasta 3 millones de datos generados por minuto a través de cámaras con IA, sensores, sensores de ruido y túneles en las líneas de las factorías que permiten verificar desde un desperfecto con una pieza o el ensamblaje, hasta monitorear el traslado de componentes de los proveedores.
La planta española de Renault en Palencia, donde se fabrican sus modelos del segmento C y D como el Austral, Espace y Rafale, el grupo, tiene instalados 380 puntos conectados a lo que la compañía denomina su Plan Connect. Este espacio de visualización en tiempo real de indicadores de calidad, costes, plazo, consumo de energía y seguridad, permite a las plantas de Renault mejorar su eficiencia, según apuntan desde la marca. El sistema, que cuenta con 8 pantallas, emite alertas operativas en tiempo real y acciones predictivas para solucionar problemas que la factoría pueda tener en ese momento.
Este hub en la planta palentina, al que ha tenido acceso elEconomista.es, funciona como un cerebro coordinador y utiliza tecnología del metaverso que le permite tener una visión global de los procesos de producción en siete etapas: pedidos, proveedores, logística de piezas, producción y logística de entrega y de vehículos desde la fábrica a los clientes. "En nuestras plantas, la tecnología actúa como eje transformador, permitiéndonos procesar 5.000 millones de datos diarios en todo el mundo para optimizar nuestro proceso productivo", ha comentado la gerente de Estrategia y Costes de Entrega en el Polo de Fabricación Iberia de Renault Group, Beatriz de Dios.
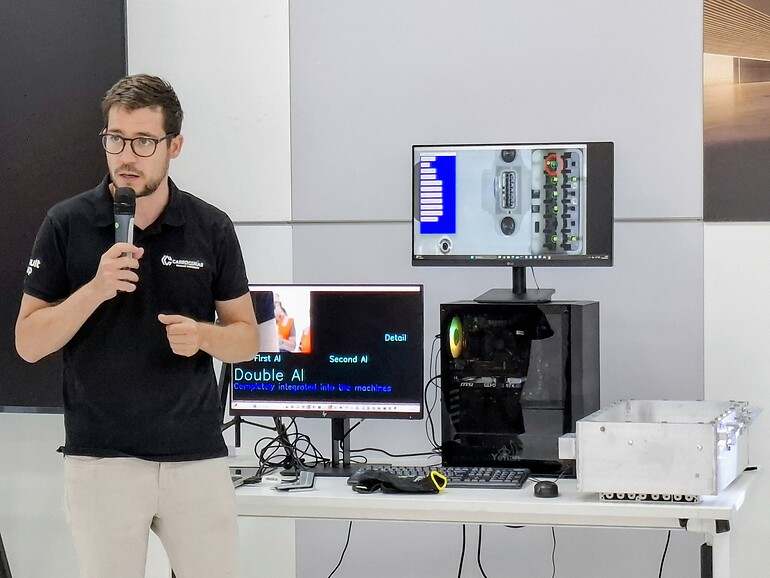
Las fábricas españolas del grupo, que llevan más de medio siglo funcionando, representaron el 14,5% de la producción total del grupo francés. Ambas instalaciones ensamblaron 350.000 unidades el año pasado, produciendo la mitad de vehículos híbridos del fabricante el año pasado. De hecho, sale de las líneas casi un vehículo por minuto, y han pasado de tener hace dos años un túnel de control de calidad y análisis con IA, a más de 70, según han explicado desde la fábrica.
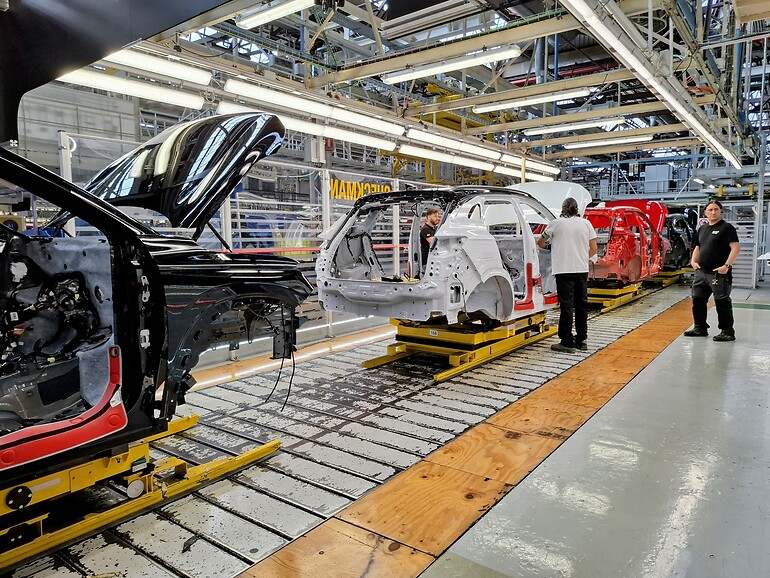
La digitalización y mejora de sus plantas ha sido parte del nuevo objetivo industrial de Renault para poder competir con los grupos de automoción asiáticos. Para avanzar en el campo tecnológico, el grupo francés, que actualmente se encuentra en búsqueda de un nuevo CEO, ha firmado alianzas e invertido en startups como Wandercraft para implantar estas nuevas herramientas en sus fábricas de todo el mundo. Estas mejoras han permitido ahorros calculables para la compañía, como la reducción de gasto energético, pasando de 1,29 MWh por vehículo en 2023, a 1,17 MWh este año, con el objetivo de llegar a 1,12 MWh. También reducir emisiones de CO2, consiguiendo una reducción de 49 KgCO2e por unidad en dos años.
Para conseguir avanzar en esta estrategia, la compañía ha permitido la entrada a otros grupos de automoción como Geely -con quien ha desarrollado la 'joint venture' de fabricación de motores Horse-, Polestar o Nissan. "Hemos dado la bienvenida a otras compañías para mitigar nuestros costes, tenemos una asociación con Geely también en Corea del Sur, donde tendremos un nuevo modelo Micra, y también para Sudamérica para desarrollar vehículos juntos. Tenemos un proyecto con Nissan basado en el nuevo Twingo... Y esto se basa en la capacidad de ser muy flexibles y de minimizar los costes de entrada", ha señalado el director de Industria y Calidad de Renault Group, Thierry Charvet.
Desarrollar un coche en dos años
Para lograr alcanzar a los fabricantes de automóviles chinos, que han duplicado su cuota de ventas en Europa en el último año, Renault cree que tienen que mejorarse los tiempos de desarrollo de los vehículos. Charvet ha explicado que la compañía ha pasado de producir los nuevos modelos del Captur o el Megane en cuatro años a tres, con el Rafale o el R5 el año pasado al Twingo, que fue presentado en 2024 y se espera que se lance el siguiente año.
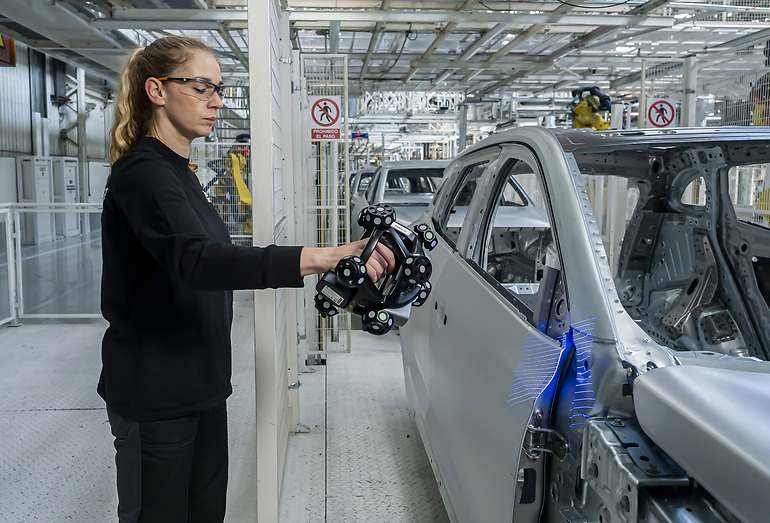
"Para el desarrollo del Twingo, el grupo Renault se ha tomado 2 años en comparación con los 4 años que tomaba crear un nuevo coche. El Twingo es un nuevo referente para nuestro desarrollo… Hemos aprendido de China, porque lo que está claro, y lo que tenemos que reconocer es que la manera china de producir coches es más rápida que lo que hacíamos antes", ha añadido el jefe de Industria de la compañía.
Charvet ha destacado que los grupos chinos cuentan con beneficios locales "debido a un ecosistema muy organizado, es decir, que las especificaciones para un componente pueden ser las mismas sin importar el coche final o la marca final… Así que ahorran mucho tiempo, pero todavía tendrá que pasar algún tiempo en Europa, porque hablamos de un continente, no de un de país, y hay muchas autoridades de por medio. Así que son rápidos porque el ecosistema los ha ayudado a ser en esto, pero hemos entendido que han conseguido mejorar su diseño y sus procesos en paralelo, y eso queremos".
Por tanto, para el directivo, es importante que todas las actividades industriales del grupo estén "totalmente sincronizadas" para mejorar la calidad. Asimismo, con Twingo el grupo buscará producir por sí mismos algunos componentes del modelo, como el panel de la puerta, los asientos o el salpicadero para reducir coste, al tiempo que ha conseguido acotar el número de partes que necesitará el modelo.