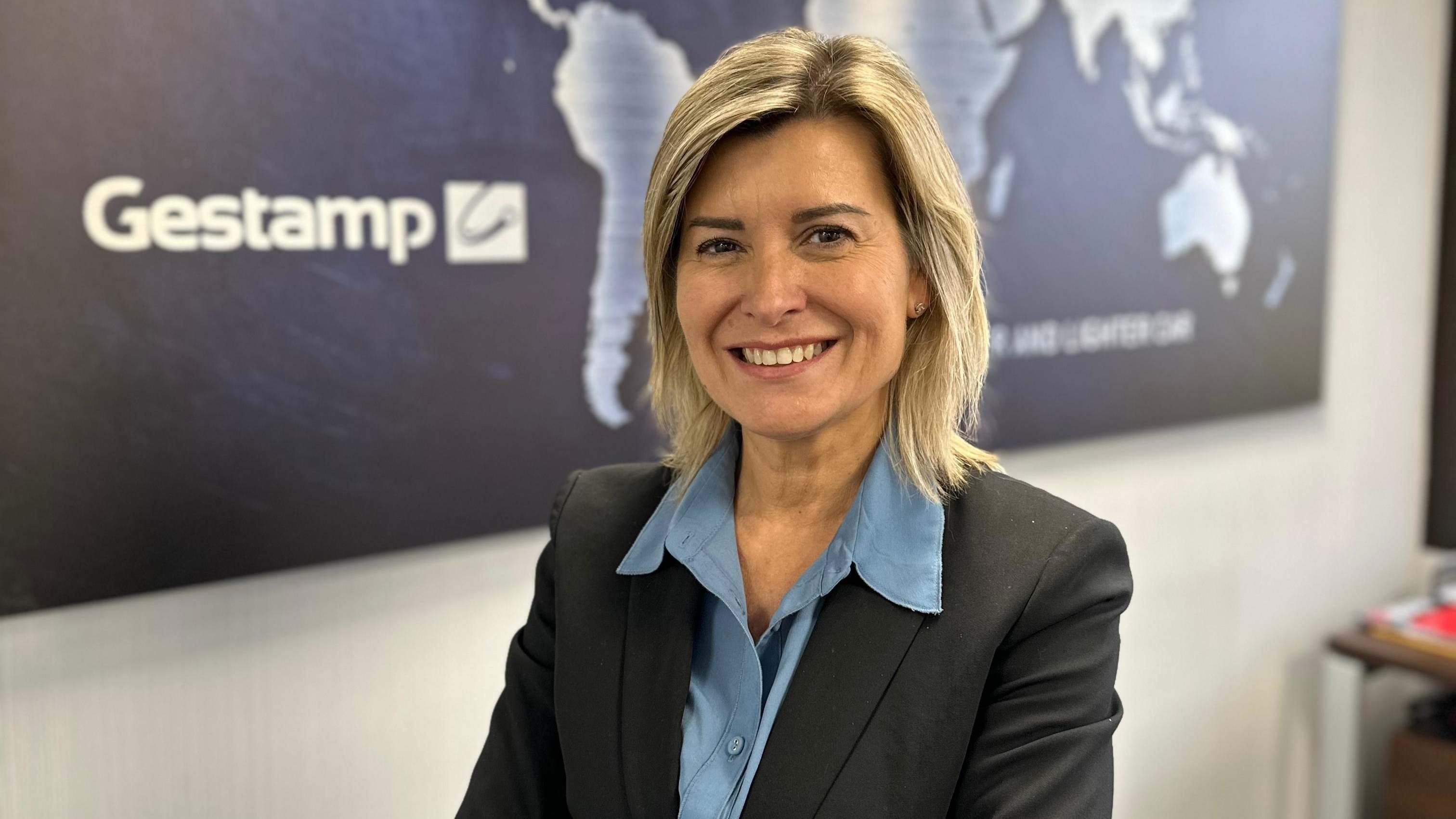
Con más de 20 años de experiencia en la automoción como ingeniera industrial, Inmaculada Domínguez es desde hace poco más de un año la directora de Innovación de Gestamp, uno de las grandes grupos españoles de la industria auxiliar del automóvil, con cerca de 1.700 personas dedicadas al área de I+D+i.
¿Qué retos supone para un proveedor del automóvil como Gestamp una revolución como el vehículo eléctrico?
La electrificación conlleva una nueva arquitectura, no solo es cuestión de meter una caja de batería con energía debajo del piso del coche, sino que toda la estructura del vehículo cambia. Para Gestamp esto es una oportunidad de ayudar a nuestros clientes a diseñar y a fabricar coches que tienen que seguir siendo seguros. Ahora, además de proteger a las personas, tenemos que proteger a las baterías. Y son coches que tienen que ser mucho más eficientes, con exigencias más altas que los de combustión y, a la vez, no olvidando que tienen que ser coches sostenibles.
Con el coche eléctrico, ¿la prioridad en innovación es reducir peso para compensar el de las baterías?
Hasta la electrificación en Gestamp trabajábamos en tres áreas de desarrollo del coche: carrocería, chasis y mecanismos. Con la electrificación también hemos entrado en cajas de batería, con lo cual abarcamos una gran posibilidad de componentes. Reducir peso significa no solo tener más autonomía con la misma cantidad de energía, sino que a la vez es menos consumo de materia prima y eso significa directamente bajar la huella de CO2. Somos una compañía que siempre hemos tenido soluciones en esa vía de aligerar. Ahora hemos añadido la sostenibilidad, con la investigación en nuevos materiales.
¿Ya están trasladando esas mejorar en innovación a la producción y a los coches?
Hemos acabado 2023 con más de 500 codesarrollos con nuestro clientes fabricantes para vehículos o plataformas eléctricas. En esos proyectos nosotros estamos diseñando junto a sus equipos de ingeniería donde. toman las decisiones. Tenemos 13 centros de I+D a lo largo del mundo, desde Japón, China, India y Estados Unidos a Europa. En esos centros ayudamos a nuestros clientes a llevar nuestras nuevas tecnologías y nuestras soluciones patentadas a sus vehículos.
¿Tienen ejemplos de éxito de esos desarrollos propios de Gestamp en electrificación?
Para el coche eléctrico hemos desarrollado una familia de productos de estampación en caliente, un área en la que llevamos más de 20 años siendo líderes y en que tenemos más de 100 plantas. Entre ellas, hemos ideado un componente en que somos capaces de integrar funcionalidades para las que hasta ahora era necesario unir distintas piezas. Eran componentes que para los coches de combustión interna se fabricaban soldando desde 9 hasta 25 piezas. Ahora somos capaces de estamparlas o fabricarlas de un solo golpe como una única pieza. Con esa solución somos capaces de aligerar un mismo sistema entre un 10% y un 15% sin cambios drásticos en producción. Al ser capaces de ofrecer una pieza única a nuestros clientes eso supone también mejoras dentro de su logística interna y le ayuda a producir coches en una cantidad menor de horas. Todo va en esa línea no sólo de reducir el peso, sino, sobre todo, de hacer coches más eficientes.
Con la electrificación Gestamp ha entrado en esa nueva línea de cajas de baterías, ¿qué oportunidades les aporta?
Con el coche eléctrico surgió la caja de baterías o battery box, que es una pieza compleja por tecnología, por los materiales y porque tiene que ser una pieza estanca. A la hora de diseñarla hay que tener en cuenta que tiene que poder contener la temperatura y el fuego en caso de un posible incendio. Esa nueva pieza nos ha ayudado a ofrecer soluciones con las que ya contábamos para otras áreas del vehículo. No solo damos el diseño, hemos ofrecido nuestro expertise en procesos de fabricación de piezas complejas con materiales como aluminio y acero. Hoy tenemos proyectos para clientes en Norteamérica, Europa y Asia. Y además de clientes que venían del mundo del automóvil de combustión, también lo hemos desarrollado para nuevos fabricantes puros de eléctricos.
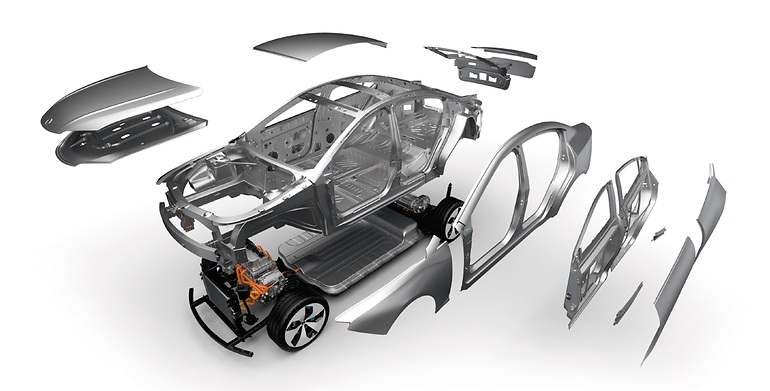
¿Cuáles cree que son las asignaturas pendientes en materia de innovación en el coche eléctrico?
En cuanto a la innovación de producto, todavía hay algún campo. Pero sobre todo es en las innovaciones en procesos donde queda mucho terreno, los procesos deben ser cada vez más sostenibles y flexibles. Nosotros también desarrollamos procesos internos para llevar la flexibilidad al máximo exponente, utilizando por supuesto la industria 4.0. El reto que tenemos todos, tanto los constructores como los proveedores, es ser capaces de fabricar, desarrollar y fabricar esos coches de manera más sostenible y eficiente.
En esa eficiencia, ¿también se incluye el coste, que de cara al cliente sigue siendo el gran handicap?
Por supuesto. Sobre todo tenemos que ser capaces de que los coches eléctricos sean asequibles para el cliente final. Los fabricantes y proveedores llevamos ya años trabajando en esas nuevas fábricas para que sean más flexibles.
Con el fuerte crecimiento de sus marcas de eléctricos, da la sensación que China está ganando la carrera en innovación. ¿Esa impresión se percibe dentro del sector?
La verdad es que China inició la electrificación de una manera explosiva. Con movimientos de fabricantes que hacían vehículos de combustión, pero también empezaron a aparecer otros muchos y pequeños, incluso fabricantes de teléfono hacen coches eléctricos en China. Es un mercado importante de desarrollo del coche eléctrico, pero no podemos minusvalorar qué está haciendo Europa. Aquí hay un conocimiento y una experiencia en el automóvil desde hace muchísimos años. Tenemos una industria de la automoción muy fuerte y es un bastión. Europa quizás haya podido empezar un poco más tarde, pero estamos absolutamente convencidos de que está avanzando y vamos a tener plataformas eléctricas de coches al mismo nivel o superior de lo que se puede ver en cualquier área del mundo.