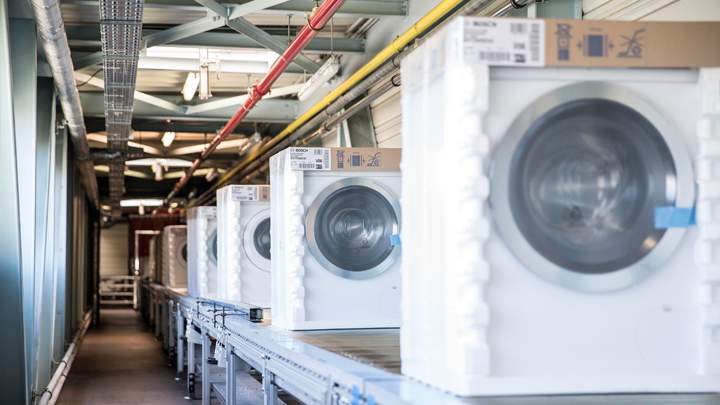
La compañía aragonesa está implementando una solución que permite ahorrar tiempo de trabajo gracias a un algoritmo con el que se automatizan procesos que, anteriormente, se han venido realizando de forma manual. La solución ya se utiliza en el centro de la compañía de electrodomésticos en Navarra y se está trabajando para su introducción en los 40 centros de BSH Group en el mundo.
De diez días de trabajo de un ingeniero a seis minutos al mes con la tecnología. Esta es una de las principales ventajas del algoritmo desarrollado por Predictland, empresa zaragozana especializada en ciencia de datos, que ha aplicado la inteligencia artificial, entre otras tecnologías, en la clasificación de los boletines de los servicios técnicos postventa de la planta de BSH Electrodomésticos España en Esquíroz, en Navarra.
El algoritmo ha permitido agilizar y automatizar el análisis de los boletines técnicos de los electrodomésticos en reparación en modo fallo (postventa) que se llevan a cabo en el Departamento de Gestión de Calidad. "Antes solo analizábamos un número concreto de boletines técnicos y, ahora, podemos analizar más. Además, antes solo analizábamos los del primer año de garantía, y ahora, podemos los dos años y adicionales", apunta Unai Esparza, Head of Field Quality Analysis en BSH Electrodomésticos España, a elEconomista
Este trabajo se hacía de forma manual con el fin de extraer información útil en profundidad, teniendo que realizar además la traducción de los boletines porque son redactados por el técnico que hace la reparación en la vivienda por lo que están escritos en diferentes lenguas. En función de la información del boletín, se realizaba la clasificación. "Era una labor tediosa que precisaba de diez días solo para analizar. Queríamos acortar el tiempo", añade. Esta necesidad de agilizar todo el proceso era necesaria porque se trabaja con entre 2.000 y 2.500 boletines, fallos y dudas de instalación de electrodomésticos de frío y lavavajillas al mes.
El algoritmo registra un 95% de acierto en los boletines de lavavajillas, que tienen más de 130 tipos de fallos distintos, teniendo un porcentaje menor de duda que el de las personas que realizaban esta función. La ventaja de este sistema, que forma parte del denominado proyecto ARIS, ha ido más allá porque ha permitido eliminar el cuello de botella del Departamento de Calidad de la planta. "Ahora, todas las personas y el departamento de Calidad, ingenieros, producción... pueden acceder a los datos de calidad de mercado y saber cuáles son los temas más preocupantes. Está todo accesible de forma sencilla e interactiva", permitiendo ver así los puntos de mejora de la fabricación o de una pieza concreta de un aparato. "Se acerca más el feedback del mercado a las personas", añade Esparza
"Antes no íbamos al detalle de los fallos porque se necesitan muchas horas de ingenieros y, ahora, se hace el trabajo con más seguridad y eficiencia", apunta Javier Alemán, responsable de Calidad de las plantas de Frigoríficos y Lavavajillas en BSH Electrodomésticos, Fábrica de Esquíroz.
"Al realizarse de manera más inteligente, hace que el proceso sea más independiente de las personas y el equipo pueda dedicarse a otra cosa de más valor" e, incluso, llevarse a cabo, aunque ellos no estén, incide Javier Alemán.
El ahorro
El algoritmo ha permitido así ahorrar 120 días de trabajo anuales, lo que supone 30.000 euros al año en tiempo de trabajo en la planta de Esquíroz. Un ahorro que puede ser mayor para la empresa, ya que el potencial se cifra en 500.000 euros con la implementación en las 45 fábricas de BSH en el mundo.
De momento, ya se han dado más pasos para implementar este sistema en otros centros como los de Montaña y La Cartuja, ambos en Zaragoza, así como en Santander. En concreto, en esta última planta se está introduciendo para las cocinas de gas al mismo nivel que en Esquíroz, mientras que en los centros de Zaragoza se está avanzando en lavadoras y en las cocinas de inducción para, posteriormente, introducirlo en los hornos, indica Javier Orús, director y cofundador de Predictland.
La aplicación de este sistema no solo se acometerá en los centros de BSH Electrodomésticos en España, ya que está a punto de implementarse en las más de 40 fábricas de BSH Group en el mundo. Entre las que mayor interés han mostrado están Polonia y Alemania. Una extrapolación que es posible porque el algoritmo ofrece posibilidades en todos los terrenos. Además, en centros como el de China, se fabrican lavavajillas que son similares y su aplicación igualmente sería factible.
La innovación
Para dar respuesta a las necesidades del centro de BSH, Predictland desarrolló dos soluciones. Una de ellas se basa en algoritmos de clasificación automática de servicios técnicos de reparación basados en tecnologías de machine learning, deep learning, Python, procesamiento natural del lenguaje, minería de texto y AWS Translate Service para la traducción automática de diferentes idiomas al inglés, incluyendo, por ejemplo, el chino.
Además, se ha trabajado en visualización integrada tanto de los resultados obtenidos del proceso de clasificación como de otras fuentes de datos de producción relacionadas con índices de calidad. En este caso, el desarrollo se ha basado en la tecnología Tableau Desktop/Server (herramienta de BI). Los datos utilizados -en ambas soluciones-, han sido del histórico de servicios técnicos de reparación y de producción relacionados con la gestión de la calidad.