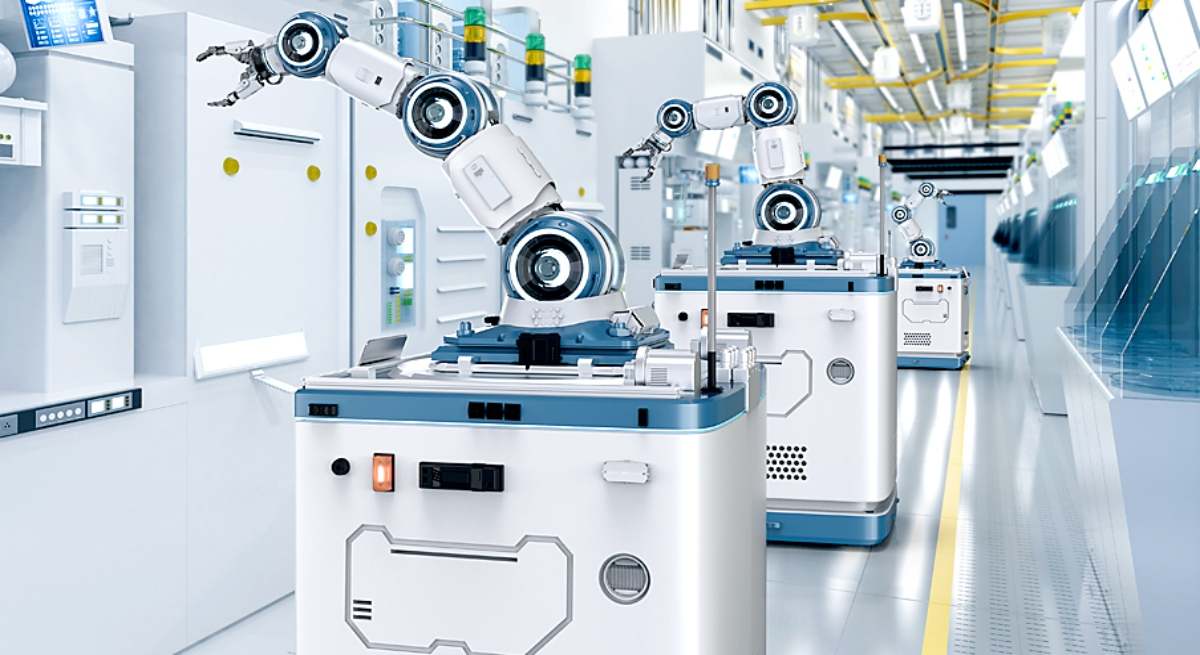
Un proceso de convergencia tecnológica en Internet entre las capacidades de procesamiento masivo de datos en tiempo real y unas telecomunicaciones de mayor velocidad y ancho de banda están dando paso al nuevo tejido industrial del siglo XXI: adaptable, eficiente, sostenible. La adaptabilidad no está exenta de complejidad, en cuanto la industria conectada requiere de la integración de diversos sistemas de operación y de gestión dirigidos a la correcta ejecución de tareas de los procesos asociados, a la generación de registros y a la optimización de las primeras, con un tratamiento inteligente de los datos.
Las cadenas de valor emergentes en la industria conectada están lideradas por el responsable de la actividad -que actúa como promotor con criterios técnicos y económicos- y las componen ingenierías de procesos e instalaciones, los proveedores de aplicaciones ajustadas a los requerimientos funcionales así como de recursos auxiliares como los "gemelos digitales", el gestor de la conectividad inalámbrica, que puede ser un operador o el mismo promotor en el supuesto de utilizar WiFi u otras tecnologías que no demanden espectro licenciado, como 5G, más el proveedor de la capacidad de procesamiento de la información, de no hacerlo por sus propios medios el promotor, que habitualmente será un proveedor de almacenamiento y computación "en la nube" de Internet. La experiencia muestra que el alineamiento de tantas y diversas capacidades para la obtención de los resultados buscados no es sencillo.
Es necesaria una comprensión única de los objetivos, hitos y entregables, asociados a la consecución o mejora de métricas de negocio y no a los rendimientos individuales, una coordinación de tareas conforme a una secuencia y unos presupuestos poliédricos contra los que medir la creación de valor financiero y los impactos de otro orden asociados. La combinación de capacidades está resultando en la aparición de modelos de gestión "mixtos", con una división "a medida" de competencias y responsabilidades entre el promotor y otros intervinientes, para ganar en agilidad y capacidad de reacción ante la generación de resultados. Sirva como ejemplo conocido de una industria en avanzado proceso de digitalización la integración de actividades para la implantación de sistemas de videovigilancia móvil en el transporte colectivo, que demanda aspectos técnicos en la calibración de dispositivos y la conectividad con una resolución mínima garantizada extremo a extremo, la comunicación entre agente y supervisor/centro de control/agente en alerta, procesamiento y almacenamiento de la información con las restricciones legales correspondientes en cuanto al visionado y custodia de imágenes, con objetivos que atienden a un interés público y a metas de eficacia y ahorro de recursos.
La especificidad de cada implantación altera la importancia relativa de las contribuciones. Así, la ingeniería es determinante para una aproximación completa, precisa y ajustada a las necesidades del promotor y las capacidades de la cadena de valor. El operador, de requerirse su intervención, será normalmente el del promotor, si bien como proveedor indirecto de equipamientos, aplicaciones y procesamiento de datos puede desarrollar una función complementaria que normalmente redunda en un ahorro de costes al aprovechar condiciones comerciales más favorables. Cada vez son más los operadores que tienen una orientación hacia el negocio de la "red como servicio" ("NaaS" en su acrónimo en inglés), que permite, aprovechando la adopción de conectores abiertos (APIs) la integración de aplicaciones de propósito concreto con flexibilidad y agilidad, en línea con el reciente anuncio de "VORA", el servicio para empresas de Vodafone en España.
El análisis económico del proyecto normalmente lo lleva a cabo el promotor, si bien cabe que la ingeniería o el operador puedan realizarlo, concretamente cuando su remuneración esté relacionada con la consecución de objetivos financieros, así como de la creación de valor desde otras perspectivas que forman parte de la nueva visión integrada de las empresas, asociadas al resto de capitales a preservar e incrementar: intelectual, social, medioambiental.
Dos artículos recientes, el primero en The Economist de 25 de marzo titulado A digital gold mine y el segundo de Rana Forohaar en Financial Times de 27 de marzo titulado A new technology boom is at hand, ponen de relieve las perspectivas de digitalización, automatización y eficiencia en procesos industriales, tomando el relevo de la innovación orientada en los últimos tiempos a la oferta al gran público de servicios y experiencias digitales. Se pone de manifiesto que la conjunción de la revisión exhaustiva de procesos para obtener mejores rendimientos, con herramientas de diseño y optimización como las desarrolladas por Celonis llevará presumiblemente a la expansión de los mercados actuales al permitir acceder a los mismos bienes o servicios en condiciones más competitivas. Más importancia quizás tenga el hecho de que modelización de los procesos de diferentes industrias permitirá su implantación en empresas de tamaño muy inferior al de las que hasta ahora tenían capacidad de adaptación e innovación en las operaciones, contribuyendo a la "localización" de la actividad manufacturera que exigen los compromisos de los gobiernos y de las empresas para la descarbonización de la economía.
En definitiva, la ahora si parece inminente y masiva digitalización industrial, de la que forman parte el rediseño de patrones, la revisión de rutinas y la conectividad inteligente asociada al procesamiento masivo de información para la mejora de prestaciones tendrá impactos profundos en los sistemas económicos, implicando una reconsideración del talento y su relación con los procesos de selección, capacitación y evaluación de las personas en el ámbito laboral, la remuneración del capital financiero invertido en base a parámetros que irán más allá del beneficio de las operaciones, para reconocer la creación y acumulación de capital intelectual en los actores económicos y la respuesta a los desafíos para la preservación del medio ambiente.
La simbiosis entre empresas líderes en sus respectivos sectores y la multiplicidad de propuestas de nuevas iniciativas empresariales para mejorar los rendimientos de las primeras caracteriza el relevo tecnológico al que estamos asistiendo. La aplicación de mejores prácticas industriales a través de los proveedores de aplicaciones es una evolución del modelo de licenciamiento tan extendido en tareas comunes, de administración en sentido amplio, ofimática y colaboración (ERP), de gestión comercial (CRM) y en particular de operaciones y suministros (SCM), aunque es demasiado pronto para valorar la complejidad de su implantación. A esta nueva generación pertenece Celonis, una empresa que surge del trabajo de investigación de un grupo de ingenieros de la universidad tecnológica de Múnich (TUM) y que fue acogida en el vivero de "start-ups" de SAP, el gigante del software alemán, hasta llegar a ser el proveedor del módulo de "process mining" de la propia SAP, cuyas aplicaciones utilizan la mayoría de las grandes empresas y un buen número de administraciones públicas europeas.
En paralelo, infinidad de nuevas empresas están desarrollando soluciones sectoriales que se mueven alrededor de dos vectores: la réplica virtual de los entornos de fabricación o logística -a través de los gemelos digitales- y la conectividad inalámbrica de elementos productivos u operativos, dotados de cierta autonomía y mayoritariamente gestionados con aplicaciones que emplean el protocolo de internet y están alojadas en las "nubes" públicas, cada vez más próximas a las operaciones, con el fin de reducir al mínimo el retardo y dar al flujo de informaciones, instrucciones y verificaciones la instantaneidad propia de agentes autónomos.
Probablemente la aproximación más estructurada a las oportunidades alrededor de la industria conectada se encuentre en Japón, una economía industrial altamente desarrollada, carente en talento cualificable a causa de su deterioro demográfico y empeñada en competir en los mercados internacionales en función de los atributos diferenciales de sus productos y de la eficiencia de sus procesos industriales. En este sentido, el operador japonés NTT viene publicando informes anuales dedicados a la industria conectada en el último de los cuales, describe la coyuntura económica incierta asociada a las secuelas de la pandemia global y a la prevalencia de conflictos geopolíticos que tienen impactos notables en las cadenas de suministro y abastecimiento y en las decisiones sobre la ubicación de las sedes del conocimiento y de las instalaciones industriales (por ejemplo, en el caso de la primera empresa del mundo por capitalización bursátil, Apple, las primeras están principalmente en California en cuanto la fabricación y distribución se basan en el Sudeste asiático). La clave de lo que el informe de NTT llama "vitalidad digital" es la sintonía entre lo físico y lo digital, que se conseguiría con una conjunción acertada de cinco elementos: la conectividad ubicua de dispositivos autónomos -también conocido como internet de las cosas o "IoT" en su acrónimo en inglés-, la transferencia de información desde el punto de acceso de red de telecomunicaciones más próximo al dispositivo y la nube en la que se trata la información ("edge-to-cloud" en inglés), la conectividad 5G, con la capilaridad que asegure la fiabilidad y rendimiento de la transferencia de datos en la frecuencia apropiada para una cobertura de interiores, normalmente sujeta a riesgos de interferencias en los entornos industriales, la optimización de los datos relevantes para la actividad en cuestión (por ejemplo, rendimiento de la operación, calidad de producto o mantenimiento predictivo de equipamiento) y actualización permanente de los patrones de fabricación en función de la aplicación de mecanismos de predicción, simulación y revisión de procesos.
La dificultad de lograr un desempeño sincronizado en los cinco elementos descritos explica que solo dos de cada cinco responsables de sistemas y tecnología de las empresas industriales de la muestra manejada por NTT crean disponer de una solución optimizada para cumplir las expectativas internas en torno a la industria conectada, que por otro lado es vinculada por más del 60% de los primeros ejecutivos de las mismas empresas con su adhesión a los objetivos de desarrollo sostenible, en lo que concierne a la reducción de la huella de carbono parcialmente a través de la digitalización y el despliegue de redes privadas de 5G, que más del 85% de los consultados estiman sustituirán en los próximos años, por razones de seguridad y fiabilidad, de tal modo que dos de cada tres estarían considerando la implantación de esta conectividad antes del final de 2024. En lo que se refiere a los avances en inteligencia artificial y robótica, las tres prioridades de los primeros ejecutivos japoneses son la mejora de la eficiencia, es decir de la automatización de rutinas operativas, el enriquecimiento de la analítica de datos y la reducción en los tiempos de resolución de contactos e incidencias, a lo que presumiblemente podrían llegar a contribuir las capacidades de reconocimiento de lenguaje natural y la aplicación de herramientas de inteligencia artificial generativa, como el popular "ChatGPT" de OpenAI.
El carácter experimental de buena parte de las tecnologías asociadas a la industria conectada -en lo que concierne a 5G, las limitaciones prácticas a la separación de niveles de servicio y la escasez de sensores adecuados restringen las implantaciones a entornos consolidados de robotización como el ensamblado de piezas, el control de flujos logísticos en circuito cerrado y las cadenas de plegado, ensamblado, envasado o precintado, éstas últimas tareas de bajo valor añadido que disuaden del esfuerzo e inversión demandados por la nueva industria conectada. La conexión de dispositivos autónomos no será la única forma de digitalizar los procesos industriales. Antes y quizás simultáneamente, la llamada "asistencia remota a operadores" representa una oportunidad que aprovecha la intuición y reflejos de las personas que ejecutan tareas predefinidas y además de su menor complejidad y coste de implementación tiene el potencial de contribuir al mayor valor añadido del trabajo. En efecto y según se ha podido comprobar en numerosos pilotos asociados a tareas de mantenimiento preventivo, de lectura de registros o de instalación y reparación de equipamientos, la asistencia remota, aprovechando utilidades básicas de realidad aumentada y la triangulación de agente-gestor-centro de control, aporta notables ahorros en capacitación y tiempos de ejecución, en campo y en la administración de repositorios de información asociados, que se benefician de la instantaneidad de las comunicaciones móviles a las que aludía el informe de NTT. La asistencia remota a operadores es la evolución natural de la conectividad de agentes con dispositivos inalámbricos que realizan tareas de control mediante la lectura de códigos de etiquetas (de barras, bidimensionales, RFID) incorporados a elementos físicos para su trazabilidad, ejecutando tareas en un entorno híbrido (mediante la superposición virtual del gemelo digital visible al agente sobre el elemento físico asociado) que evita actuaciones de mayor coste.
Las agendas inversoras de los países industrializados y notablemente de la UE prevén para los próximos años cuantiosas ayudas a la digitalización del tejido productivo y a la conectividad industrial. En España la Agenda Digital 2026 contempla en su eje 6, para la digitalización de PYMES un presupuesto de 5.000 millones de euros, especialmente a través de las ayudas para el "kit digital", al tiempo que el impulso a 5G se beneficia de un presupuesto de más de 1.514 millones de euros y algunos proyectos de digitalización sectorial como el agroalimentario y el del ciclo del agua está previsto que sirvan como tractores de este proceso de modernización productiva que el presidente del Foro Económico Mundial, Klaus Schwab, bautizó como la cuarta revolución industrial.
Alberto Horcajo es cofundador de Red Colmena