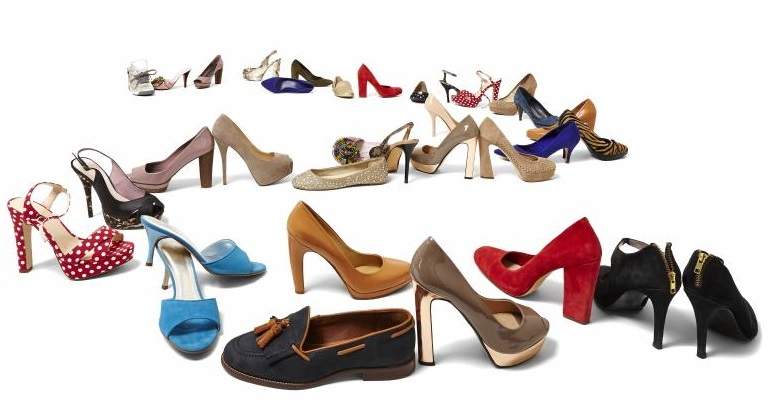
Un grupo de empresas alicantinas ha unidos sus fuerzas para desarrollar la factoría del futuro, capaz de plantar cara en costes a China gracias a la tecnología y recuperar parte de la producción que se deslocalizó con la globalización.
La industria zapatera concentrada en la comarca de Elche aspira a recuperar parte de la producción de calzado que en las últimas décadas ha emigrado a países de bajos costes laborales, fundamentalmente de Asia. Y su principal aliado para lograr esta deslocalización a la inversa es la tecnología. El objetivo es desarrollar una factoría 4.0 que sea capaz de reducir los costes de fabricación a niveles de sus rivales asiáticos.
Un ambicioso plan que une a patronales como la Federación de Industrias del Calzado de España (Fice) y la de componentes de calzado Aeecc, fabricantes como Pikolinos o el proveedor Zahonero, y firmas tecnológicas y de otros sectores. En total 46 empresas y entidades participan en el proyecto Eco Challenge, presentado a la convocatoria del Ministerio de Industria para la identificación de los Proyectos Estratégicos para la Recuperación y Transformación Económica (Perte) que buscan financiarse con los fondos Next Generation EU.
El zapato, como otras industrias eminentemente manufactureras como el juguete o el textil, fue uno de los productos que inició el proceso que ha permitido a China llegar a ser la fábrica del mundo. Unos menores costes laborales para los que ahora sí que hay una receta. "Añadiendo tecnología y cambiando y simplificando procesos podemos conseguir un volumen de producción a unos costes que nos permitirá recuperar una parte de la industria", asegura Ezequiel Sánchez, director general del proyecto.
Sánchez, que fue director general adjunto durante casi una década de la mayor firma del calzado de Elche, Tempe, filial de Inditex, se marca un objetivo ambicioso: reducir en un 30% el coste de producción de cada par de zapatos.
Más productividad
Para el ejecutivo, uno de los problemas del calzado ha sido que para ser competitivo en precio ha concentrado su estrategia en los costes de mano de obra y se ha olvidado de la productividad. "Lo que tenemos que conseguir es una industria con más valor añadido. La tecnología nos va a ayudar a ganar productividad y eficiencia en los costes, además de poder gestionar toda la cadena de valor. Ahora la parte productiva retiene muy poco de la cadena de valor que genera el calzado, mientras que la parte comercial y la final es la que se queda con la parte más importante".
El proyecto que aspira a los fondos europeos no se basa en una única tecnología y suma 15 ejes distintos de mejora de las industrias actuales del calzado. El esqueleto principal de esa fábrica futurista es la tecnología 3D Bonding, desarrollada por la alicantina Simplicity Works y clave para reducir el coste respecto a la fabricación a mano, ya que elimina la mayoría de los cosidos de los zapatos. A través de una unión química de polímeros y su inyección en un molde logra producir en un solo paso la mayoría de la estructura del zapato o la zapatilla.
La idea del proyecto es complementarla con otras tecnologías en que ya trabajan otras empresas del sector o de otros ámbitos para generar más competitividad en toda la cadena. Así, también abarca la introducción de nuevas tecnologías para la gestión de todos los procesos. Una de las empresas que participa es la empresa de robótica Asti, para abordar el despliegue industrial de robots autónomos para el transporte interno dentro de las fábricas, una solución que no se está utilizando en el calzado, pero ya se aplica en otros sectores.
Otra de las apuestas del proyecto es su sostenibilidad, ya que el proyecto considera que para garantizar la competitividad de la fábrica no sólo será fundamental su tecnología, sino también su capacidad de no generar residuos y de reciclar. "Hay que tener una visión sistémica de toda la cadena de valor para ver como integrar diseño, materiales, la parte de producción y comercialización, y con sistemas de información para que todo sea más ágil" explica Sánchez.
Planta piloto en septiembre
Un primer embrión de este proyecto será la creación de una planta a escala piloto, denominada fábrica LAB o fábrica laboratorio, en la que Simplicity Works invertirá 2,5 millones de euros. Una inversión prevista antes de que se anunciaran los fondos europeos y que se armase todo el proyecto, por lo que se prevé que pueda estar operativa en septiembre en Elche con independencia de los fondos europeos.
Este centro piloto dará trabajo a más de un centenar de profesionales y tendrá capacidad para 600.000 pares de zapatos anuales. Su función principal es demostrar que la tecnología 3D Bonding es viable a escala industrial y que los operadores puedan tocar una fábrica real.
Los fondos europeos permitirían acelerar las siguientes fases de un proyecto que prevé una inversión de 170 millones hasta 2026. En un horizonte de entre dos y tres años se espera consolidar un centro industrial que permita la fabricación anual de 3,6 millones de pares de zapatos y un millar de empleos. En 2026, el objetivo sería producir 24 millones de pares con 8.000 empleos ligados. Una cifra que supondría casi una cuarta parte del volumen total que se produce actualmente en España, que roza los 100 millones de pares.
Además de las posibilidades tecnológicas de reducir costes existen otras tendencias mundiales que soplan a favor de esa vuelta de la producción a España. Lo ocurrido en Europa con la falta de suministros sanitarios ha subrayado los riesgos de depender de cadenas de suministro a mucha distancia. Otro factor a tener en cuenta será el cada vez mayor coste de la huella de carbono del transporte.