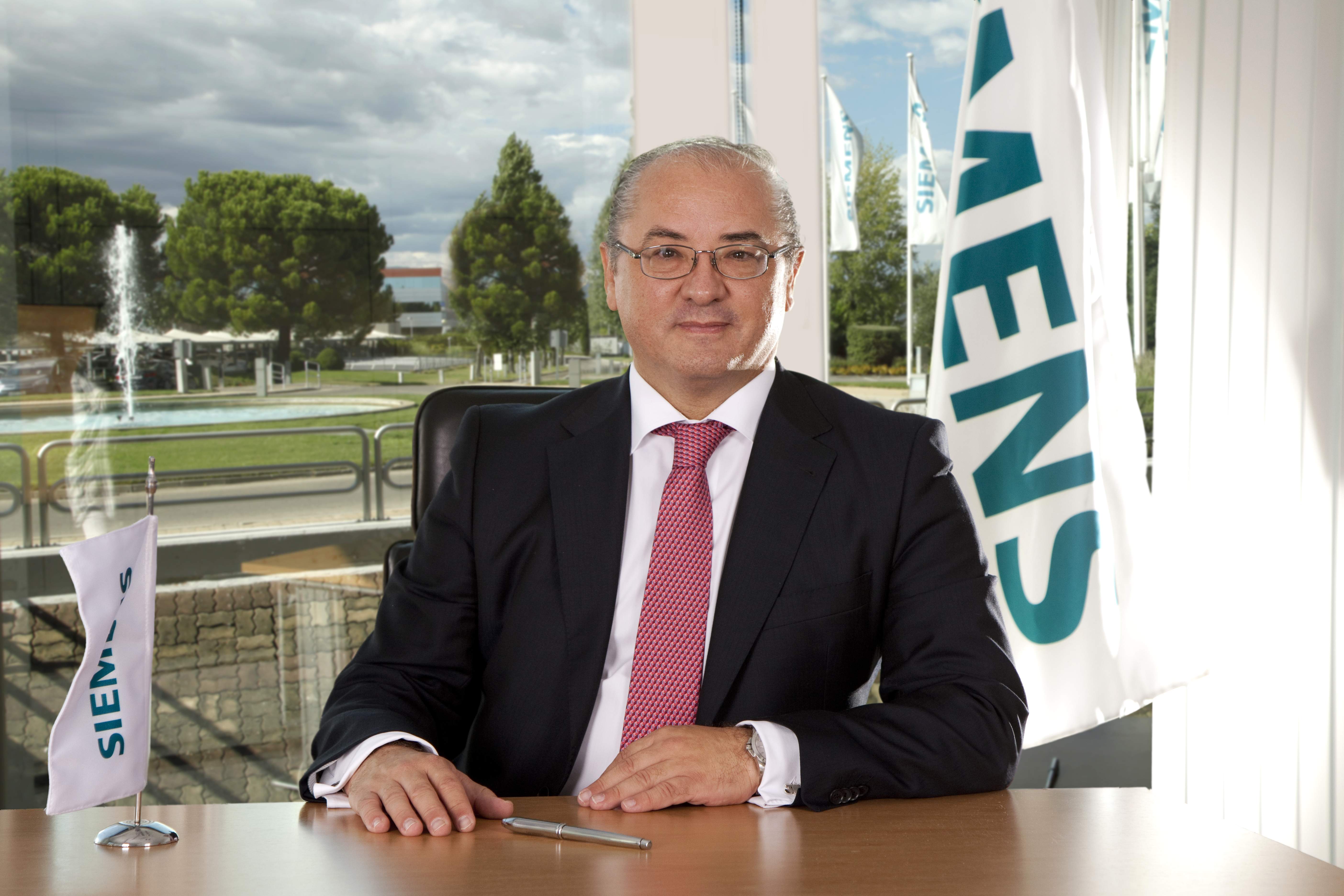
Juan Miguel Pérez de Andrés, director general de Siemens Energy Managment, está desarrollando un proyecto transformador en las fábricas de Gestamp para mejorar su eficiencia energética.
¿Cómo está evolucionando su acuerdo con Gestamp?
Firmamos una alianza para mejorar el consumo energético en sus plantas. Se trata de un proyecto global para sus más de 100 fábricas en todo el mundo. A finales de diciembre de 2017, se instaló el sistema de monitorización en la planta China de Dongguan. En breve, estará operativo en tres factorías más: dos plantas en Aragón y otro sistema más en la República Checa y antes de que finalice el año, se instalará en otras 4 factorías chinas con lo que alcanzaremos ya las 22 plantas.
Hicimos un primer piloto para ver la viabilidad del sistema, que está basado en la utilización del Big Data y a partir del análisis de los datos dar recomendaciones que en primera instancia son para ahorrar energía pero que finalmente han ido más allá ya que tiene una parte de beneficios operacionales como la detección temprana de problemas en maquinaria, mantenimiento predictivo o la monitorizacion en tiempo real a través de un portal web que permite al cliente comparar máquinas similares en plantas diferentes o ver qué máquina está teniendo un comportamiento distinto al esperado o las mejores prácticas de una máquina comprada al mismo proveedor.
¿Qué beneficios produce?
Tiene unos beneficios económicos como la trasparencia del coste de los procesos y con ello puedes saber el coste real de energía que tiene una pieza y donde antes se hacían promedios ahora se tiene una mayor trasparencia para ver a nivel analítico la huella de carbono. Este servicio además detecta procesos ineficientes como prensas que se quedan conectadas por la noche cargando el hidráulico sin producir ninguna pieza. Gestamp ha declarado ahorros de varios millones de euros, hasta un 15 por ciento en las plantas ya instaladas, que son la punta del iceberg porque lo que ellos buscan es la excelencia operacional con la eficiencia y ahorro.
¿Y cómo evoluciona?
Es un sistema que tenemos preparado para ellos con la monitorizacion y con informes personalizados así como alarmas y avisos en función de los parámetros que nos indican. Hay una colaboración muy estrecha de su personal y nuestro equipo. Les vamos dando los informes que nos solicitan.
¿Se pueden utilizar en otros negocios estos sistemas?
No es un sistema exclusivo para el automóvil. Todos los procesos pueden mejorar su eficiencia. De hecho, tenemos otros clientes con los que estamos arrancando ahora mismo la colaboración. La eficiencia energética es un reto que tenemos todos. Están desde las ayudas básicas para cambiar las ventanas o las luces led hasta acciones muy avanzadas ligadas a la operación. En la fábricas de Gestamp incluso se ha mejorado la iluminación con respecto a lo que tenía, lo que te permite mejorar. La eficiencia energética en mi opinión personal es un punto que está todavía por alcanzar su madurez.
¿Cómo funciona el centro de control que tienen en Sevilla?
Se instaló un centro de control para dar servicio a estos clientes. Ahora mismo controlamos más de 600 MW. Adicionalmente, hemos sido nominados como Mainsphere Aplications Center para realizar aplicaciones para nuestra red. En el mundo hay 22 centros y estamos orgullosos de que sea reconocido nuestro equipo de desarrollo. Más de 900 especialistas en datos e ingenieros están ya trabajando junto a los clientes de Siemens en estos centros para desarrollar innovaciones digitales para análisis de datos y machine learning. Siemens quiere sacar partido a la base instalada de dispositivos que tiene en todo el planeta.