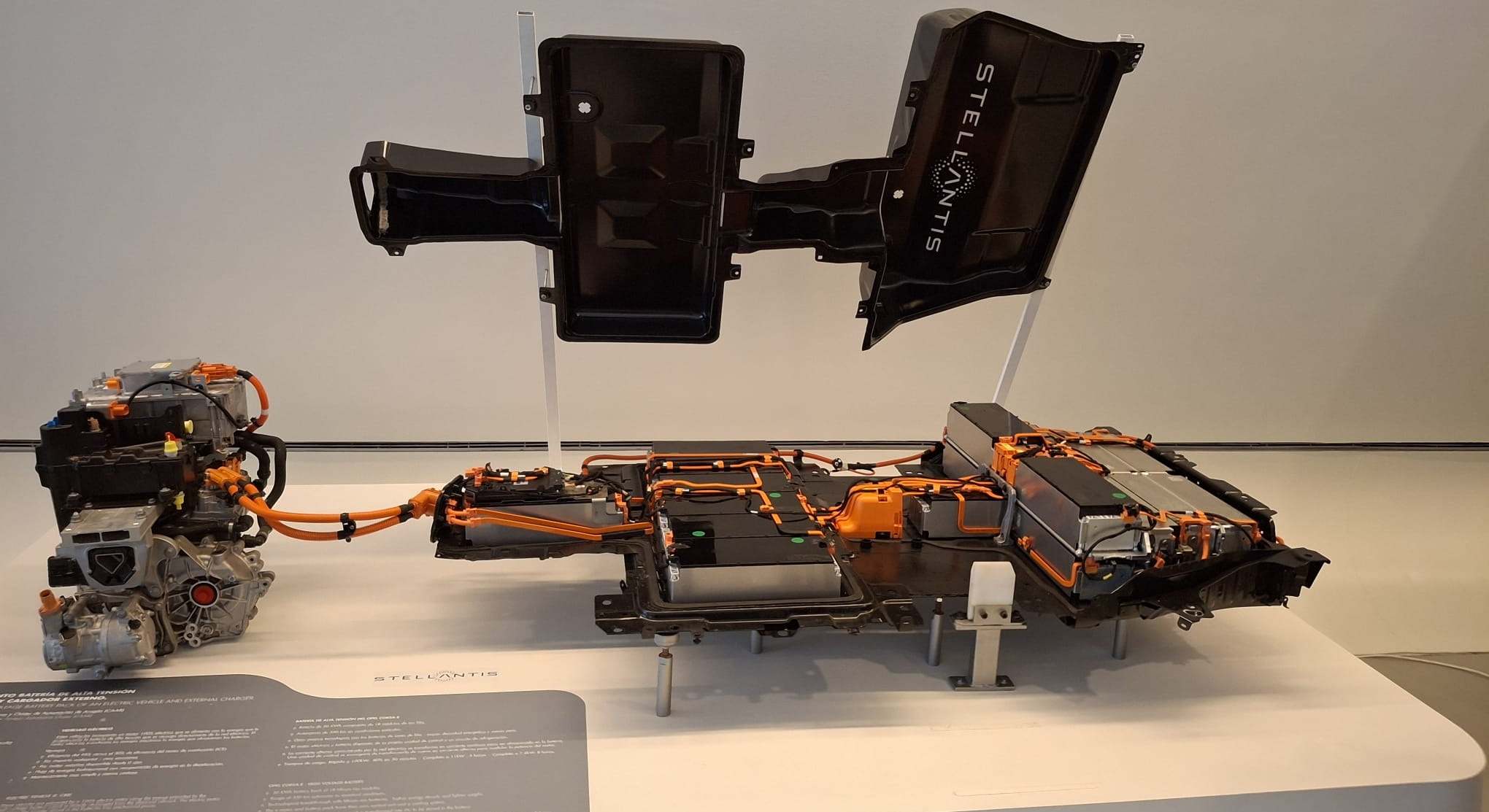
El coche eléctrico y la instalación de la gigafactoría de baterías para estos vehículos de Stellantis y CATL en Figueruelas, en Zaragoza, abre nuevas oportunidades de negocio al tejido industrial de Aragón con el fin de poder disponer de las diferentes piezas y componentes que se emplean para la fabricación de estos vehículos y no solo para los modelos de la planta zaragozana.
Y, para conocerlas, nada mejor que ver in situ todos componentes y parte de los vehículos eléctricos para poder observar cómo son de primera mano, conocer su diseño y materiales empleados y analizar las posibilidades de fabricación en las empresas situadas en Aragón. Una demostración que se ha podido ver en el evento 'EV Revolution: batteries and global trends', organizado por el Cluster de Automoción y Movilidad de Aragón (CAAR) y en el que han participado alrededor de 200 empresarios.
El chasis del Tesla Model Y, para observar cómo en una sola pieza se ha producido una parte clave del chasis del vehículo para albergar la batería, que anteriormente se realizaba en 20 pasos; la battery pack del Opel Corsa de Stellantis y todas las piezas de un vehículo eléctrico de BYD que, por primera vez se han mostrado en España, así como su batería eléctrica, que llega a tener un peso de unos 460 kilos. De esta marca china, se han conocido además "las entrañas" los vehículos BYD Dolphin y el BYD Seal.
Además de los piezas y componentes, las empresas también han podido explorar los procesos con la tecnología gigacasting (fundición inyectada), que por ejemplo, emplea Tesla con la que se reduce peso y tiempo de producción y que se está incorporando ahora en Europa, aparte de observar cómo impacta en los componentes estructurales o BIW (body in White), en piezas reales tanto de Tesla como de otras marcas líderes en el sector.
Un conocimiento que tiene un especial valor actualmente, dado que en España se están construyendo varias gigafactorías de baterías, como la de Stellantis y CATL en Zaragoza, que abren puertas para la diversificación de la actividad de las empresas y poner en marcha nuevas líneas de negocio para suministrarlas a los diferentes fabricantes de coches eléctricos. Además, los fabricantes chinos han puesto sus ojos en Europa y, en España, como es el caso de Leapmotor.
"Hemos organizado este evento para conocer el vehículo eléctrico, sus diferentes partes, baterías y motores que mueven el vehículo eléctrico", ha explicado Juan Carlos Dueñas, vicepresidente de Innovación del Cluster de Automoción y Movilidad de Aragón, quien ha incidido también en la necesidad de que las empresas innoven en productos para dar respuesta a los retos de fabricación de los vehículos eléctricos.
Un proceso en el que Aragón tiene una posición privilegiada dentro de Europa que, además, se ve acentuada por la gigafactoría de baterías, que puede facilitar que "los propios proveedores den el salto y que vengan proveedores externos" con la tecnología y piezas que todavía no se están produciendo en la comunidad aragonesa, en la que ya se montan baterías en la planta de Figueruelas en Zaragoza y de la producción de adherentes que se incorporan en ella para unir las celdas, que son fabricados por Convenzar.
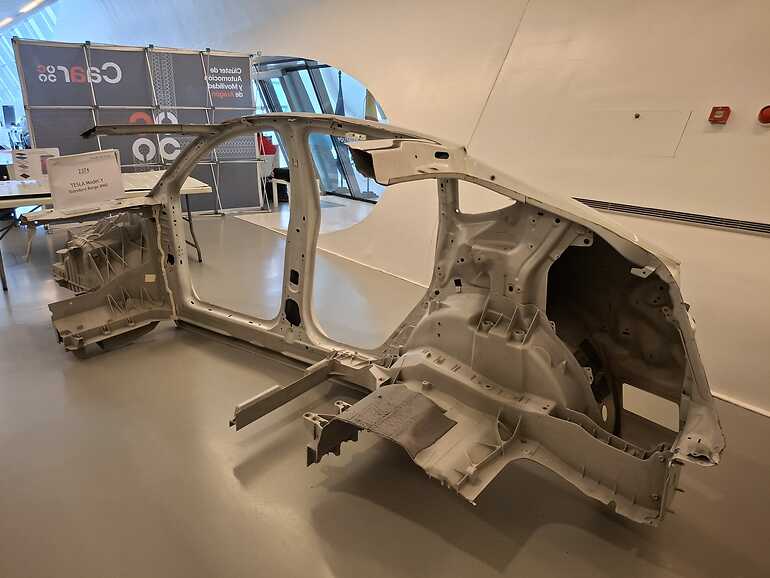
Y los retos son numerosos porque no solo se necesitan piezas plásticas o de otros materiales. También el coche eléctrico requiere de más electrónica y también de más tecnología, sobre todo a nivel de software, para optimizar la conducción y la eficiencia de estos vehículos de la mano, por ejemplo, de la inteligencia artificial, que permitirá adaptar la conducción al suelo por el que circule el vehículo y a las condiciones meteorológicas. Será una conducción inteligente que, además, redundará a su vez en una mayor autonomía, que se calcula que podría aumentar en unas dos horas.
Precisamente, tanto la electrónica como esta parte de tecnología, a nivel de software de gestión, son los grandes retos para las empresas en Aragón, pero también el resto de componentes y de la batería, segmento este último que se espera que despegue en la comunidad aragonesa con la puesta en marcha de la gigafactoría en Figueruelas, en horizonte de 2027-2028. "Los proveedores ahora conocen mejor las baterías y pueden participar en su fabricación" tanto para las que emplee Stellantis como las que se suministren desde esta planta en Zaragoza a otras marcas de automoción en Europa.
"Se trata de crear una cadena de valor en torno a las baterías", ha añadido David Romeral, gerente de CAAR, quien ha explicado que hay muchos retos en el sector como conseguir aunar más autonomía con menos peso de la batería y de los componentes.
"El coche eléctrico tiene mucha electrónica, más que el tradicional, y de esto, en Aragón, no tenemos mucho", ha incidido Romeral durante este evento en el que se ha podido conocer la transformación en algunas piezas en las que se está sustituyendo el cobre por el aluminio o la mayor necesidad de refrigeración de un vehículo eléctrico, que abren nuevas oportunidades, al igual que las piezas metálicas, las plásticas como el punto para recargar el coche o los cableados, de los que se necesitan más de 100 metros para un solo vehículo eléctrico. Otras piezas clave son las ruedas, especialmente las llantas, por la aerodinámica, o los discos de freno.
"Nunca hemos hecho todo esto para el coche eléctrico y tenemos que aprender", ha señalado David Romeral, quien ha apelado a aprovechar estas oportunidades y el momento de la fábrica de baterías de Stellantis y CATL, sobre la que ha ahondado en su importancia por "retener lo que ya tenemos -en relación a la planta de Figueruelas-, generar un nuevo centro de producción (la gigafactoría) y poder crear una cadena de suministro complementaria y que las empresas diversifiquen o vengan nuevas a Aragón".
Una opción que no se ha descartado desde el Gobierno de Aragón, ya que La directora general de Promoción Industrial e Innovación, Mar Paños, ha explicado que muchas empresas optan por instalarse cerca de los centros de producción, en este caso, de la gigafactoría de baterías.
Durante el evento también se han podido conocer las últimas tendencias en evolución de las baterías, como la creciente relevancia de las baterías LFP (litio, hierro y fosfato) por su competitividad y seguridad, especialmente en vehículos eléctricos destinados al consumo masivo.
También se han abordado las baterías NMC (níquel, manganeso y cobalto) de las que se ha apuntado que seguirán siendo fundamentales en segmentos premium debido a su superior densidad energética.
De la mano de diferentes ponencias, igualmente, se ha debatido sobre innovaciones prometedoras como las baterías de estado sólido, cuya escalabilidad podría transformar radicalmente el panorama energético europeo.