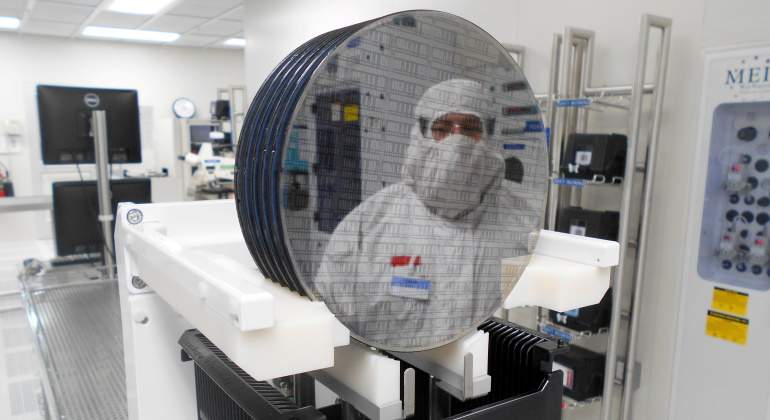
Pese a haber cerrado el primer trimestre del ejercicio con importantes beneficios en sus cuentas de resultados, los grupos automovilísticos encaran el segundo trimestre con la preocupación de no contar con semiconductores para poder producir.
Esta situación, que afecta a cerca de 42.000 trabajadores, se suma a la difícil recuperación que afronta el sector, debido a una menor demanda, fruto de la crisis económica provocada por la pandemia.
Nunca antes la industria de la automoción se había encontrado con una situación tan complicada. Sumida en una profunda transformación, con el objetivo de contar con una mayor oferta de vehículos electrificados, así como una mayor demanda de los clientes en que el producto esté más conectado, el sector cuenta con una falta de semiconductores que afecta a todas las plantas que los distintos consorcios automovilísticos tienen en todo el mundo.
Una de los primeros mandamases de la industria en alertar de esta situación fue el consejero delegado de Stellantis, Carlos Tavares. El directivo portugués reconoció en la presentación de resultados de 2020 del Grupo PSA, del que también era consejero delegado, que no se mostraba confiado en que esta situación mejorase en la segunda parte del año.
Y es que las distintas automovilísticas encaran el segundo trimestre con parones en sus fábricas. Ford, que logró cerrar su mejor primer trimestre en diez años al ganar 2.691 millones de euros, recortó sus previsiones de producción a la mitad para el periodo comprendido entre los meses de abril y junio. La explicación del fabricante norteamericano se debe a que, unido a la escasez de semiconductores, uno de sus proveedores de este tipo de chips sufrió un incendio en una de sus plantas en Japón el pasado mes de marzo. Situación que hace más complicada la recuperación del sector.
Según un estudio de la consultora IHS, se prevé que la escasez dure hasta el tercer trimestre, cuando la reasignación de la capacidad de las fundiciones de semiconductores y, posiblemente, un cierto enfriamiento de la demanda de electrónica de consumo debería proporcionar una mayor seguridad de suministro. Esta falta de semiconductores se explica por una menor demanda por parte de los fabricantes de vehículos cuando llegó la pandemia. Entonces, la industria tecnológica, aupada por una mayor demanda de ordenadores y videoconsolas debido al confinamiento, reclamó esos chips que antes requería el sector de la automoción.
La industria del automóvil trabaja con procesos just in time (justo a tiempo), que se caracterizan por una falta de aprovisionamiento con el objetivo de reducir costes. Ahora, las automovilísticas se están viendo obligadas a reformular estas estrategias, de la misma manera que algunos estados han movido ficha para solventar esta situación. Es el caso de Estados Unidos. El presidente norteamericano, Joe Biden, se comprometió a destinar 50.000 millones de dólares para apoyar la investigación y fabricación de chips con el objetivo de rivalizar con China.
En la misma línea se pronunció a finales de abril el secretario general de Industria y Pyme, Raül Blanco, dependiente del Ministerio de Industria, quien pidió a Europa que reforzase su soberanía industrial para poner fin a la escasez de semiconductores.
Ante esta situación, la alternativa sería construir más fábricas que pudiesen surtir al mercado. Pero no es tan sencillo. Según un informe de Boston Consulting Group, la producción de semiconductores es muy intensiva en capital. Así, instalar una fábrica de semiconductores de última generación con capacidad estándar requiere entre 5.000 y 20.000 millones de dólares de gastos de capital, incluyendo terrenos, edificios y equipos. Esta cifra es mucho mayor que el coste estimado de un portaaviones de última generación (13.000 millones de dólares). Así, los gastos de capital de las empresas dedicadas a la fabricación de semiconductores suelen suponer entre el 30 y el 40% de sus ingresos anuales. ¿Y para qué se necesitan estos chips? Sus usos en la industria de la automoción son variados. Desde los sistemas avanzados de ayudas a la conducción, denominados ADAS, hasta el sistema de infoentretenimiento, pasando por el chasis o los sensores de memoria, que son los encargados de alertar sobre los niveles de presión, inercia o humedad.
Tal es la importancia que, según un estudio de AlixPartners, esta escasez costará este año a la automoción 110.000 millones de dólares y reducirá la producción mundial en 3,9 millones de vehículos. En el primer trimestre del año -últimos datos disponibles- las ventas mundiales de semiconductores aumentaron un 17,8% en tasa interanual, hasta los 123.100 millones de dólares, lo que supone un 3,6% más interanual, según datos de la Asociación de la Industria de Semiconductores (SIA, por sus siglas en inglés).
Situación en España
Desde que se inició la pandemia, la situación patria en el sector de la automoción no ha sido buena. Tan solo en los meses de julio y diciembre del pasado año las matriculaciones de vehículos nuevos consiguieron un crecimiento o mantuvieron el mismo nivel de ventas que en el ejercicio anterior. Ahora bien, la subida del impuesto de matriculación el pasado enero y la no continuidad del plan Renove -del que tan solo se emplearon 50 millones de los 250 disponibles-, ha provocado que en el primer cuatrimestre del año tan solo se hayan comercializado 264.655 unidades. Es decir, un 39,3% menos en comparación con las ventas logradas hace dos años, según datos de la patronales de fabricantes (Anfac), concesionarios (Faconauto) y distribuidores (Ganvam).
Esta situación ha desatado una ola de Expedientes de Regulación Temporal de Empleo (Ertes) en las distintas factorías españolas, debido a la escasez de semiconductores. Lo cierto es que esta situación está afectando a todas las plantas de los distintos grupos automovilísticos y da buena muestra de la dependencia que padece Europa de Asia en estos asuntos. Y es que cuando se aplicaron los confinamientos el año pasado los fabricantes de vehículos dejaron de demandar estos productos. En ese momento, el sector tecnológico se quedó con esos chips que dejó de necesitar el automóvil. El problema vino cuando se reanudó la actividad y los productores de estos semiconductores no daban abasto para surtir tanto a los fabricantes de vehículos como al sector tecnológico. A lo largo de todo el año se han llevado a cabo distintos Ertes debido a la falta de suministro. En total, hasta la fecha hay afectados por este tipo de expedientes cerca de 42.000 trabajadores de las plantas españolas.
La última planta en padecer un Erte ha sido la que el grupo Stellantis tiene en Figueruelas (Zaragoza), cuyos más de 5.000 empleados se verán afectados hasta final de año. El acuerdo al que ha llegado la dirección y los sindicatos contempla 50 jornadas de paro es decir, 250 turnos de trabajo, y no podrán superarse a título individual un máximo de 80 días de suspensión por empleado.
Igualmente, la factoría que Stellantis tiene en Vigo también sufre la misma escasez. Por ello, la dirección y los sindicatos acordaron a finales de marzo un Erte para 3.749 trabajadores, de los más de 7.000 con los que cuenta la fábrica de Balaídos. Este paro estará vigente hasta final de año y cubrirá un máximo de 60 días laborables a los trabajadores con contrato a tiempo completo.
La primera en llevar a cabo un Erte fue Seat. La automovilística, propiedad del Grupo Volkswagen, firmó a mediados de enero un Erte para 550 trabajadores, que podría afectar a un máximo de 11.000 empleados hasta finales de junio. Dirección y sindicatos acordaron que el Erte se levante el próximo 30 de mayo en la fábrica de Martorell y en Seat Barcelona, un mes antes de lo previsto, mientras que se mantendrá hasta el 30 de junio en Seat Componentes. Según los sindicatos, este Erte ha provocado que se dejen de producir en la planta catalana 24.000 vehículos.
En la misma situación se encuentran las plantas de Sevilla, Palencia y las dos de Valladolid. Dicho expediente se extenderá hasta el 30 de junio en Sevilla y hasta el 30 de septiembre en Palencia y Valladolid. En total, afecta a 9.163 trabajadores de Palencia y Valladolid y a otros 1.000 de Sevilla.
Volkswagen Navarra, por su parte, mantiene activo el Erte que puso en marcha el año pasado y que afecta a 5.000 trabajadores. De hecho, la planta de Landaben tuvo que paralizar la producción los pasados 24, 25 y 26 de marzo por este motivo.
En el caso de Ford, la planta de Almussafes parará la producción durante 20 días hasta el 31 de julio, medida que afectará a 6.400 empleados. Además, el resto de días laborables, al no producir Transit hasta julio y la desaparición temporal del turno de noche (hasta ese mismo mes de julio), habrá unos 1.400 trabajadores en Erte diariamente. En julio, cuando se recupere la producción de la Transit, esta cifra se reducirá a los 600 empleados diarios.
Menor producción
Esta situación se traduce en una menor producción en las plantas españolas. En los tres primeros meses del año se ensamblaron 662.224 vehículos. Pese a que esta cifra es un 2,3% más que hace un año, supone un 12,5% menos en comparación con 2019. Todo ello obedece, según la patronal Anfac, a una menor demanda de los mercados europeos, en especial el propio español, y al desabastecimiento de semiconductores en las fábricas.
Alemania, cuarto fabricante mundial y primero europeo, ha producido 933.617 vehículos en el primer trimestre del año, según datos de la Asociación de la Industria del Automóvil (VDA, por sus siglas en alemán). Esto supone un 8,4% menos en tasa interanual y un 26,2% menos en comparación con las cifras de hace dos ejercicios.
La falta de chips se suma a una lista de contratiempos con los que lidia el sector desde que se inició la pandemia. Aunque las previsiones del consenso de mercado que reúne FactSet estiman un beneficio conjunto de los principales grupos automovilísticos de 79.000 millones de euros para este año, un 32% más desde que se anunció el antídoto de Pfizer.
Más contratiempos
Por si la situación no fuese delicada hay que añadir algunos contratiempos que se han producido en los últimos meses, lo que ha complicado la situación en algunos proveedores de estos chips. El taiwanés TSMC, el mayor fabricante de chips del mundo, advirtió en su último informe anual que "las tensiones comerciales podrían conllevar a un incremento en los precios de los equipos clave o incluso a su falta de disponibilidad".
Por su parte, Renesas, otro de los grandes proveedores, sufrió en marzo un incendio en una de sus plantas japonesas, lo que obligó a paralizar la producción de chips. La compañía nipona prevé que la producción en esta planta reanude las entregas a niveles normales para principios de julio. A todo ello hay que sumarle que Samsung Electronics, otro de los grandes fabricantes, sufrió en Texas (EE.UU.) una ola de frío que le obligó a parar la producción durante un mes, lo que ocasionó unas pérdidas por valor de hasta 360 millones de dólares en daños. Actualmente, la planta de Austin ya está operativa.