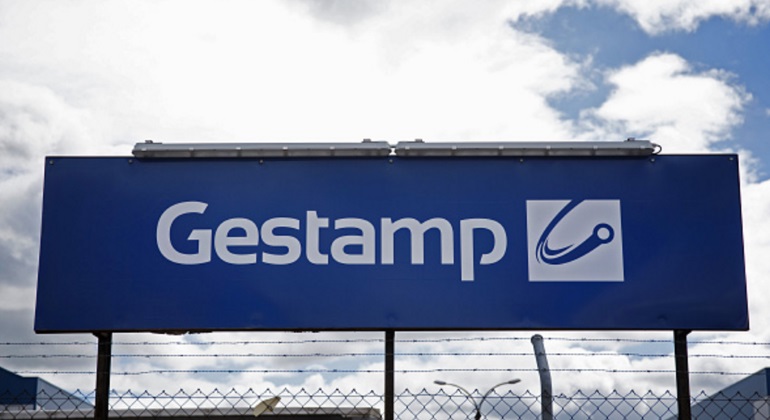
El sector de la automoción es a buen seguro el que mejores ejemplos ofrece de últimas tecnologías aplicadas a la producción. "Nosotros no confundimos industria 4.0 con automatización, ya que la automatización la hemos vivido y la aplicamos siempre que podemos. Por ello, nuestros procesos son bastante inteligentes ya de por sí". De esta manera nos lo explica René González, director de manufactura avanzada y estandarización de equipos de Gestamp. Esta multinacional española cuenta con 100 plantas industriales en 20 países y 13 centros de I+D y está especializada en el desarrollo y fabricación de componentes metálicos -carrocería, chasis y mecanismos- para firmas como Daimler, Hyundai o Toyota. Con 41.000 empleados, facturó 8.202 millones de euros en 2017. "Una línea de producción con 100 robots tiene mucha complejidad y mucha inteligencia. Cuesta mucho añadir más inteligencia a partir de aquí. Creo que por este motivo el cambio cultural no va a ser tan importante como en otros sectores", explica este responsable de Gestamp. | Más noticias en la revista digital gratuita elEconomista Factoría 4.0.
Le preguntamos qué nota se pondría en cuanto a digitalización y dice un cuatro sobre cinco: "Si nos comparamos con otras industriales, podemos decir que estamos en una fase bastante avanzada". Ello se debe a que cuentan con una estrategia clara, con proyectos que están aportando valor, un ecosistema que permite implantar estas iniciativas de una forma estandarizada. "Si comparamos el valor que tenemos ahora con el que vemos a largo plazo, estamos en una fase embrionaria. Vemos un valor y una transformación tan grande que nos damos cuenta de que solo estamos empezando", añade.
Diferentes iniciativas
Nos explica René González que todas las iniciativas están enfocadas a ser más competitivos: "La competitividad en nuestro caso tiene que ver con la eficiencia en las operaciones. Buscamos hacer más y mejores productos con los mismos recursos", aclara. En estos momentos tienen en marcha 11 iniciativas, todas ellas combinando Big Data con análisis de datos históricos, interconexión de los sistemas y las cosas y análisis en tiempo real. Cuentan así con iniciativas de Big Data y otras donde la conectividad y el tiempo real es lo más importante. "Un ejemplo de las primeras, donde el tratamiento masivo de datos tiene mucha importancia, es una iniciativa que tiene que ver con la estampación en caliente, que es nuestra tecnología estrella, ya que es la más determinante a la hora de conseguir vehículos más ligeros y seguros. De cada línea de producción recogemos cerca de 2.000 variables, con una resolución media de 150 milisegundos, lo cual supone más de mil millones de datos por día. Tratamos de recoger todo lo que pueda tener influencia en el producto final con la idea de analizar las series de datos históricos y aprender. Esto nos sirve para fijar las condiciones que nos ayudan a predecir fallos y a mejorar el rendimiento del proceso", explica.
Un ejemplo del segundo tipo de iniciativas es la llamada logística inteligente, donde lo importante es la interconexión en tiempo real de todos los sistemas de una planta, la localización en tiempo real de los medios logísticos y un algoritmo complejo que es capaz de optimizar la logística y que sea totalmente inteligente. Con otra iniciativa buscan asegurar la calidad de los productos de chasis; otra, la más madura y con la que han conseguido ya ahorros significativos, está relacionada con la eficiencia energética. "De lo que se trata es de dar más inteligencia a los procesos y las cosas y de ir construyendo de una forma ordenada el concepto que vemos en el largo plazo y que no es otro que el de planta inteligente", añade el director de manufactura avanzada y estandarización de equipos de Gestamp.
Distintas tecnologías
En todas estas iniciativas aplican muy distintas tecnologías relacionadas con la Industria 4.0, ya sea realidad aumentada, reconocimiento de voz, robots colaborativos o todo tipo de técnicas de analítica avanzada como el machine learning o la inteligencia artificial. Sin embargo, este directivo pone el foco también en algo que nos aporta valor muy rápido y que se suele olvidar en un mundo tan complejo y tecnológico: "Digitalizar el conocimiento interno".
En cuanto a la manera de ir aplicando todas estas tecnologías a su centenar de plantas activas, nos explican que todas las iniciativas pasan por cuatro fases (concepto, piloto, despliegue y adopción), y se lideran desde un departamento centralizado que sigue criterios estándar aplicables a todos los países donde están presentes.
Aunque la transformación digital de la compañía empezó por "la voluntad clara y decidida de nuestro presidente ejecutivo" -explica González-, "diría que hoy hay centenares de responsables, desde los técnicos de las plantas que nos ayudan a sacar valor de los proyectos con su conocimiento, hasta los científicos de datos que programan algoritmos".