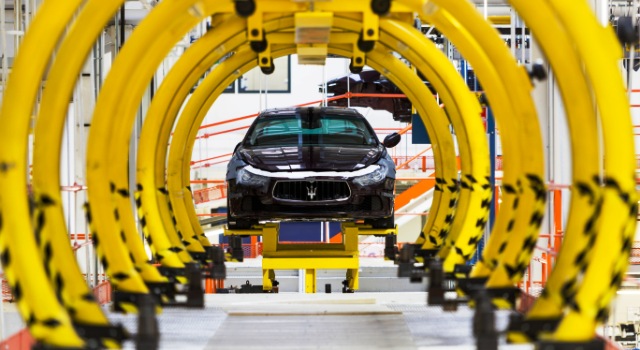
La antigua fábrica Bertone muestra cómo la digitalización puede flexibilizar la producción, aumentar la competitividad y lograr más eficiencia en los vehículos.
La planta de Maserati en Turín es uno de los mejores ejemplos de cómo las nuevas tecnologías pueden mejorar la competitividad de las empresas sin perder ni un ápice de su esencia. En ella, conviven cientos de robots rodeados de los uniformes color crema y azul marino de los 200 empleados de la planta. Sus directivos cuentan a elEconomista que son conscientes de la necesidad de modernizar sus herramientas de trabajo, en un momento en el que los fabricantes de automóviles deben adelantarse a la innovación de sus competidores si no quieren quedarse en el olvido.
El origen de la planta Avvocato Giovanni Agnelli ubicada en Gruliasco, a poca distancia de Turín, se remonta a la década de los 60 cuando el Grupo Bertone decidió convertirla en su joya de la corona. En 2009, y después de más de tres años parada y en bancarrota, el gigante automovilístico italiano por excelencia, el grupo Fiat, se hizo con ella y renovó los equipos de la planta al instalar nuevas líneas de producción. En 2013, la antigua fábrica Bertone se reabrió con la producción de dos de los modelos estrella de Maserati: el Quattroporte y el Ghibli.
Adaptación a las exigencias del mercado
Pero no sólo eso. Maserati se llevó a la planta reformada a muchos de los antiguos trabajadores de Bertone (la edad media de los empleados es de 46 años) que modificarían su antiguo rol en la empresa con la llegada de los robots. En la actualidad, esta planta tiene una capacidad de producción máxima de 50.000 automóviles al año.
No obstante, es complicado cumplir con las exigencias de rapidez del mercado sin sacrificar la calidad de los productos. Por ello, Maserati tomó la decisión de buscar un socio industrial para mejorar sus procesos, desde la fase de prototipos al vehículo final.
El elegido fue el gigante alemán Siemens. Entre otras aportaciones, cabe destacar -en la fase inicial- el "gemelo digital" o, en otras palabras, la implementación de un software creado por los alemanes que permite tener una copia del vehículo original en una pantalla. Durante la fase de desarrollo, los datos de ambos coches se usan simultáneamente, permitiendo reducir errores, coste y tiempo.
Otro avance proporcionado por Siemens está relacionado con la acústica. ¿Cúantas personas son capaces de reconocer un coche de lujo a un kilómetro sólo por el sonido de su motor? "El sonido es algo extremadamente importante para un fabricante de coches como Maserati", explicó el director de ventas en Italia de Siemens, Marco Maggi. "Los clientes asocian el sonido con la marca", argumentó Maggi. Para optimizar el sonido dentro del coche, la compañía alemana coloca un tambor equipado con micrófonos en el prototipo, que graba los sonidos para usarlos posteriormente en sus test digitales.
Modernización en todas las fases de producción
Dejando a un lado la fase de prototipos, la etapa de creación de la carrocería es una de las que más ha sido modernizada. El 75 por ciento de la línea está automatizada y en ella trabajan 85 robots. Sin embargo, estas herramientas digitales están supervisadas, a su vez, por operarios reales que comprueban que no haya ningún problema a través de diferentes pantallas. Además, el cuidado de los vehículos Maserati se respira en cada esquina de la planta y llama la atención ver cómo los operarios eliminan manualmente la suciedad del chasis, lo pulen a fondo y echan una pintura especial para que no tenga ninguna rozadura.
Otra parte muy curiosa es la nave del ensamblaje. En esta zona se ve a la perfección la convivencia entre las nuevas tecnologías y los seres humanos. Los coches suben y bajan, los robots los giran, los acercan y los alejan. Mientras, los operarios preparan la suspensión, los amortiguadores o, incluso, sacan brillo al símbolo de Maserati. El director de este área explica a este diario que, cuando algún operario detecta un fallo o posible problema, toca el botón de una pantalla y comienzan a soñar diferentes melodías en forma de aviso para que la persona responsable acuda a ver qué ocurre.
Por otro lado, en la fase del acabado final, los coches son revisados uno a uno y los defectos que puedan surgir se introducen en el ordenador para conformar una base de datos y que los ingenieros puedan resolver los problemas a la mayor celeridad. Los vehículos con problemas (normalmente, un coche a la semana) los llevan a otra zona para su posterior reparación.
La combinación virtual y real en el negocio de la firma automovilística permite reducir el tiempo de desarrollo de los vehículos en un 50 por ciento, flexibilizar la producción (por ejemplo, el modelo Ghibli está disponible en 27 versiones, 13 colores y 205 configuraciones distintas) y, por supuesto, aumentar la eficiencia de la fábrica. Finalmente, el trabajo conjunto de operarios y robots en esta fábrica (es la segunda por detrás de la de Módena) da como resultado un pulido e impecable Maserati.